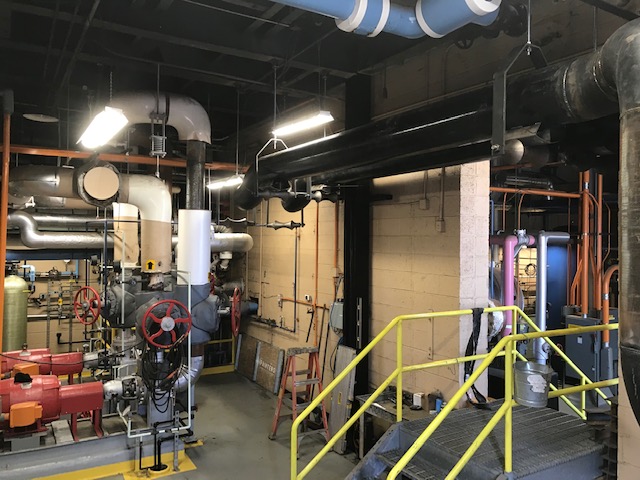
The enormous task of running our utilities at Rutgers falls to the Renovations and Infrastructure Services group led by Janice Davey, IP&O’s Assistant Vice President. The myriad of responsibilities associated with maintaining our cogeneration and heating plants, underground distribution lines, cooling systems, elevators, solar fields, and so much more, does not end there. This group also handles frequent regulatory reporting, maintenance, repairs, construction, planning, and an ongoing search for grants and rebates to help offset costs. In addition, the group oversees sustainability, carbon reduction, and energy reduction.
“We have an extensive and complicated utility infrastructure,” said Davey. “It requires 24/7 attention, constant maintenance and upgrades, and a continual search for products or programs that aid in efficiencies and cost offsets.”
Infrastructure Services is responsible for all campuses and all remote locations, as well. It is comprised of three main areas: utilities, energy management systems, and sustainability. Within these three areas are hundreds of IP&O employees who keep the university running.
Ted Elonis, Sr. Director Utilities, oversees the university’s cogeneration and heating plants on all campuses. He also manages the maintenance and repairs for the university’s buried (underground) distribution system, mechanical piping systems and equipment in buildings as it relates to utilities equipment on fired and unfired pressure valves. He also handles quality assurance of new construction of buried utilities. In addition, Elonis manages the compliance requirements including registrations, inspections, reporting, hydrants, pressure vessels, underground oil tanks (USTS), and sanitary and storm water collection systems.
“We have 24 hour shift operations state-wide including boiler operators, boiler checkers, HVAC mechanics and supervisors to make sure everything is functioning and that there are no problems through the night,” Elonis said. He also ensures that every one, of the roughly 150 utilities employees, is current on all certifications and licenses required to do their jobs.
There are eight plants that run 24/7 and require personnel on site: Busch Co-Generation Plant, College Ave. Central Heating Plant, RBHS Co-Generation Plant, SSB, ICPH-RBL, Rutgers Legacy Plant Newark, Camden Central Heating Plant, and the CHI New Brunswick Plant.
Compliance is a big part of Elonis’ job. The university’s 256 fire hydrants, for example, need annual static and residual testing and flushing. There are 1,440 pieces of equipment for which Elonis and his team are required to do annual inspections or at a frequency determined by the state. These include turbines, boilers, chillers, heat exchanges, air compressors, unfired pressure vessels, and autoclaves, to name just a few. Certificates and licenses are also required to run these units. Copies of the registered equipment must be posted at each equipment location. Emissions testing is required on some of the equipment, as is annual cleaning and inspections. Boiler plants require one to three on site stationary engineers. Unmanned boiler plants over 4 million BTUs must be checked three times in an eight hour shift. These boilers also require weekly inspections, safety valve checks, low water cut-off checks, and a blow down of each unit must be conducted to rid the system of sediment and reduce corrosion.
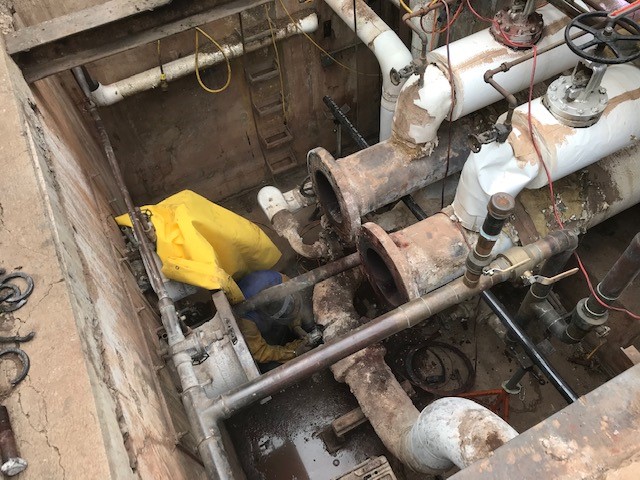
Among the many maintenance and repair items completed in-house by our utilities' workers, includes this manhole repair on Busch Campus.
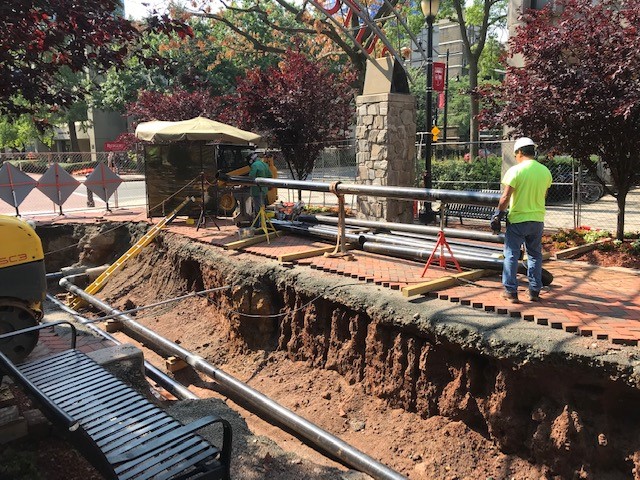
Utilities crew repairing the high temperature hot water lines on the Newark Campus.
The university also has 19 underground oil tanks (UST); each must be registered with the NJDEP. Utilities personnel are registered as either Class A, B, or C UST operators. Twenty four hour monitoring equipment is required for all registered underground tanks, and plans must be in place for spill prevention at all sites. Annual testing is required, and proper signage must be posted along with permits at each site.
Rutgers has approximately 200 miles of distribution including electric, fiber, water, sewer, storm, high temperature hot water, and compressed air and gas lines. Utilities personnel manage and perform updates to its underground utility distribution network and is responsible for surveying or documenting the underground facilities and keeping utility maps updated.
There are over 35 miles of sanitary piping and 20 sanitary collection lift systems at Rutgers. Rutgers is registered with DEP as a C-2 Waste Water Facility and must comply with all regulations. Quarterly reporting to outside agencies, twice weekly visual checks of the lift stations, and quarterly, semi-annual, and annual preventive maintenance is conducted. Emergency equipment must be maintained, on site, and readily available should an emergency arise at any hour. A 24-hour automated continuous monitoring system will alert operators of an emergency.
“DEP has been extremely satisfied with our operation of our C-2 Waste Water Facility pertaining to our lift stations and also our sanitary distribution system,” said Elonis. “They have brought new interns from DEP to this facility to show them a properly run facility. They do not visit us every year now due to the fact that our reporting and maintenance is above average. We have been put into their Stewardship program.”
The Newark RBHS and Busch Cogeneration plants recently underwent a major facelift. New gas turbine generators and waste heat recovery boilers are the latest technology added to both plants and are expected to significantly improve the reliability and efficiency of the utilities provided by those plants. “The turbine generator output combined with utility service from the high voltage switchyards have been engineered and designed in a way that provides redundancy, and a very resilient system that will keep the lights and heat on in almost any situation,” said Elonis. Recently a Factory Mutual Insurance inspector toured the sites and commented, “While touring these sites, I also noticed a general pride of ownership exhibited by the personnel which is evidenced by the excellent housekeeping, fresh paint and preservation activities throughout the plants. The Rutgers utilities department are to be commended for a job well done and a commitment to continuous improvement.”
Glenn Vliet, Senior Director Utilities Operations, oversees four shops including the chiller shop, energy management systems control shop, elevator shop, and the high voltage electrical shop.
The chiller shop is responsible for all chillers on all campuses. There are approximately 165 chiller systems and 10 miles of underground chilled water lines on the campuses. “Some of our chillers are in central plants and others are in individual buildings,” Vliet said. Chillers are one component of an air-conditioning system which keep the buildings cool. Summer time is often the time when calls come in about building temperatures. Vliet’s team is responsible for the overall operations and maintenance of the chillers and monitors and checks for any alarms indicating problems. The chillers are subject to daily inspection and preventive maintenance. “When we get a call complaining that the building is too warm,” Vliet explained, “our team determines if it is actually the chiller causing the issue or if another problem within the HVAC system has to be addressed.”
The energy management shop is charged with making sure all building controls are working properly. This group starts each day checking for any system alarms and addresses these accordingly. “We have shop personnel as well as vendor assistance, when needed, to address any issues. This is a very specific, high tech area, and our goal is to rely less on vendors and more on our own trained professionals over time,” Vliet said. Shop personnel must be knowledgeable in six different control systems.
The elevator shop is responsible for 425 elevators throughout the state. Because there is a maintenance contract with Otis Elevators, only one Rutgers employee handles the maintenance and annual testing of the elevators. “We work in conjunction with the elevator inspector who is part of Scott Luthman’s group (Codes and Standards) to do inspections and get on top of elevator issues immediately,” Vliet said. “If an issue arises that is covered under the Otis contract, then they address it. We handle anything else.”
The high voltage electrical shop is responsible for distributing power to each campus building. There are five electrical distribution systems which consist of six primary substations, multiple secondary substations, transformers, switches, and 58 miles of underground distribution on the campuses. Each campus, except legacy Newark, has a primary substation. In addition, there are other substations throughout the campuses. “The power feed comes from Public Service,” Vliet explained, “and we distribute the power through the university distribution system to each building. We feed about 98% of the buildings on our campuses.” If a problem arises in the high voltage feed, it can affect many buildings. Problems may be the result of cables, transformers, switch failures, or circuit breaker failures. “The fortunate thing about high voltage is that the distribution system has redundancy and we can re-feed the electrical power to buildings quickly. After power is restored to the buildings, we can make the needed repairs and return the system to its normal operation,” Vliet explained. “We make sure we have a lot of redundancies in the system.”
The department also manages the maintenance of 170 emergency generators which require monthly testing. Generators kick in during a power failure, and there is one with black start capability which will run the power plant should a catastrophic failure wipe out all power. “Any time we run a generator, we have to maintain a record of run hours for environmental compliance. NJDEP or the Department of Health can review these records at any time. It does not matter if it is a test run or a power failure that causes the generator to start. There are a lot of compliance requirements surrounding environmental permits on campus, so any time they run we need to file a report.” REHS helps with the reporting process.
Michael Kornitas, Director of Sustainability and Energy, oversees the procurement of natural gas, oil, electric, and water for the university, collecting the data and usage and reporting to finance department on a monthly basis. His group is also responsible for annually calibrating water meters around the Rutgers Campuses.
A big part of Kornitas’ job is to increase conservation and sustainability efforts. “Right now we are auditing 108 buildings,” said Kornitas. The audit, being conducted with PSE&G, will look for ways to reduce energy consumption in these buildings. Upgrades will include lighting and mechanical systems.
“We work with PSE&G, NJ Clean Energy, and other state and federal entities to identify grants and loans that will help us in these efforts,” Kornitas explained. Recent upgrades to the Newark RBHS cogeneration plant and the Busch cogeneration plant will help increase plant efficiency. Kornitas was very instrumental in securing the loans and grants needed for these costly projects.
Having started at Rutgers as a Planner Estimator, Kornitas also worked in building design and construction and eventually utilities. One of his responsibilities is to make sure all new buildings are at the very least certified LEED Silver equivalent. His knowledge of building design makes him a reliable partner to IP&O’s project teams.
“I would like to congratulate and express my appreciation for the hardworking utilities employees who have been on campus working tirelessly not only through the pandemic, but every flood, snow storm and nor’easter. No matter the challenge, they are here doing a fantastic job,” Davey said.
Featured in the IP&O Newsletter, May 2022.